Metal Fabrication: Creating Custom Body Panels
Discover the art of metal fabrication for creating custom body panels for your classic car. Learn essential techniques like welding, shaping, and forming. Achieve unique and personalized results.
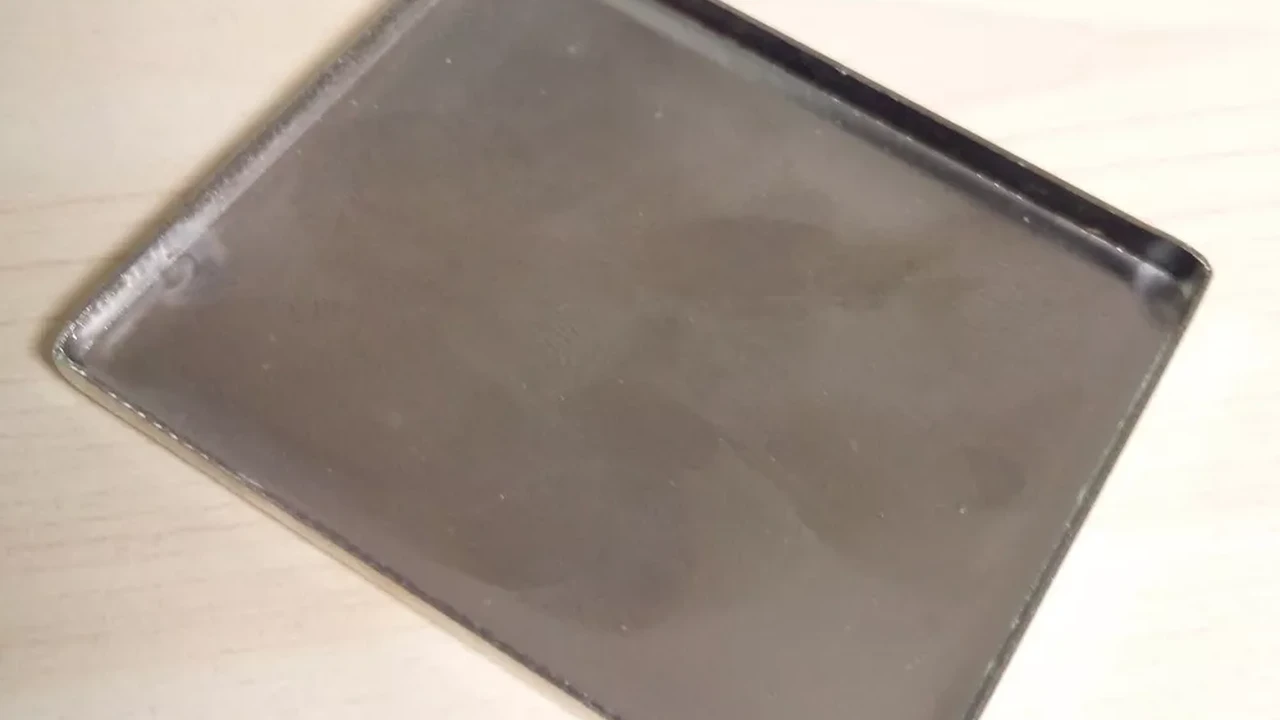
Introduction to Metal Fabrication for Classic Car Restoration Body Panels
So, you're thinking about tackling some serious bodywork on your classic car? Fantastic! Maybe you've got a rust bucket with panels beyond repair, or perhaps you're dreaming of a custom look that no off-the-shelf part can provide. That's where metal fabrication comes in. It's the art and science of shaping metal to fit your specific needs, and it can be a game-changer for your restoration project. Don't be intimidated! While it takes skill and practice, the basics are achievable, and the results can be incredibly rewarding. This article will guide you through the essential techniques, tools, and considerations for creating custom body panels, turning your vision into a reality.
Essential Tools for Classic Car Metal Shaping Fabrication
Before you start bending metal, you'll need the right tools. Here's a rundown of some essential equipment for metal fabrication, along with considerations for choosing the right ones:
- Welding Equipment: A good welder is the cornerstone of any metal fabrication shop.
- MIG Welder (GMAW): Ideal for beginners and general fabrication. Easy to learn and versatile. Consider the amperage range (180-250 amps is a good starting point) and duty cycle (how long you can weld continuously before the machine needs to cool down). Products like the Lincoln Electric Power MIG 210MPi (around $1200) or the Hobart Handler 190 (around $900) are popular choices. Use case: Welding patch panels, creating structural supports, joining fabricated pieces.
- TIG Welder (GTAW): Offers more precise control and cleaner welds, but requires more skill. Great for welding thin metals like aluminum and stainless steel, and for creating aesthetically pleasing welds. Look for features like pulse welding and AC/DC capability. A Miller Dynasty 210 DX (around $3500) is a top-of-the-line option, while the AHP AlphaTIG 200X (around $800) provides excellent value. Use case: Welding intricate details, aluminum panels, creating show-quality welds.
- Stick Welder (SMAW): The most basic type of welder, suitable for thicker metals and outdoor use. Less common for bodywork due to its potential for splatter and difficulty with thin materials.
- Cutting Tools:
- Plasma Cutter: Quickly and cleanly cuts through metal. Essential for shaping panels and removing damaged sections. Look for a plasma cutter with adjustable amperage and a pilot arc. The Hypertherm Powermax 45XP (around $2000) is a highly regarded professional-grade option. A more budget-friendly choice is the Lotos LTP5000D (around $400). Use case: Cutting out rusted sections, trimming panels to size, creating complex shapes.
- Angle Grinder: Versatile tool for grinding, cutting, and shaping metal. Use with various discs for different tasks. A 4.5-inch grinder is a good size for most bodywork applications. The DeWalt DWE402 (around $80) is a reliable and affordable option. Use case: Grinding welds smooth, removing rust, cutting metal with a cut-off wheel.
- Nibbler: For making precise cuts in sheet metal, especially around curves. A great alternative to shears for intricate work. The Malco TN1 Turbo Nibbler (around $200) is a popular choice. Use case: Cutting out complex shapes, trimming panels along curved lines.
- Shears: Hand-operated or powered shears for cutting sheet metal. Useful for straight cuts and gentle curves.
- Shaping Tools:
- English Wheel: Used to create smooth curves and contours in sheet metal. A must-have for replicating complex body panels. Look for a wheel with a variety of lower anvil wheels for different radii. A good quality English Wheel can range from $500 to $2000 depending on size and features. Use case: Creating fenders, door skins, and other curved body panels.
- Hammer and Dolly Set: Essential for shaping and smoothing metal. A variety of hammers and dollies are needed for different tasks. A basic set can be purchased for around $100. Use case: Removing dents, shaping metal around forms, smoothing welds.
- Shrinker/Stretcher: Used to shrink or stretch metal to create curves and flanges. Helpful for forming complex shapes. A combination shrinker/stretcher is a versatile tool. A good unit will cost around $200-$400. Use case: Creating flanges for welding, forming curved edges on panels.
- Planishing Hammer: Used to smooth out hammer marks and refine the shape of metal. Can be hand-operated or air-powered. An air-powered planishing hammer can range from $300 to $1000. Use case: Smoothing out hammer marks, refining the shape of panels, creating a smooth finish.
- Metal Bending Brake: For creating precise bends in sheet metal. Useful for forming flanges and corners. A benchtop bending brake is a good option for smaller projects. Prices range from $100 to $500 depending on size and capacity. Use case: Creating flanges for welding, forming corners on panels, creating brackets.
- Measuring and Layout Tools:
- Measuring Tape: Essential for accurate measurements.
- Combination Square: For marking 90-degree angles and measuring depths.
- Contour Gauge: For transferring complex shapes from one panel to another.
- Markers and Scribes: For marking cut lines and reference points.
- Safety Equipment:
- Welding Helmet: Auto-darkening helmet is highly recommended.
- Welding Gloves: Protect your hands from heat and sparks.
- Safety Glasses: Wear safety glasses under your welding helmet and when using other power tools.
- Ear Protection: Protect your hearing from the noise of power tools.
- Respirator: Protect your lungs from fumes and dust.
- Leather Apron or Jacket: Protect your clothing from sparks and heat.
Welding Techniques for Classic Car Metal Body Panel Fabrication
Welding is a fundamental skill in metal fabrication. Mastering the basics of MIG or TIG welding is crucial for joining fabricated panels and repairing damaged areas. Here are some key techniques:
- MIG Welding (GMAW):
- Preparation: Clean the metal thoroughly to remove rust, paint, and grease. Ensure a good ground connection.
- Settings: Adjust the wire feed speed and voltage based on the thickness of the metal. Practice on scrap metal to find the optimal settings.
- Technique: Use a consistent travel speed and maintain a proper welding angle. Overlap your welds slightly for a strong and continuous bead.
- Common Problems: Porosity (caused by contamination or incorrect settings), burn-through (caused by excessive heat), and lack of fusion (caused by insufficient heat).
- TIG Welding (GTAW):
- Preparation: Clean the metal thoroughly and use a back purge to prevent oxidation.
- Settings: Select the appropriate tungsten electrode, gas type, and amperage based on the metal being welded.
- Technique: Use a foot pedal to control the amperage and maintain a consistent arc length. Add filler metal as needed to create a strong and clean weld.
- Common Problems: Tungsten contamination (caused by touching the tungsten to the weld pool), porosity (caused by contamination or incorrect gas flow), and cracking (caused by excessive heat or stress).
- Seam Welding: Creating a continuous weld along a seam. Requires precise control and consistent technique to avoid distortion.
- Spot Welding: Joining two pieces of metal with a series of spot welds. Useful for attaching panels to frames and creating strong, localized joints.
- Plug Welding: Welding through a hole in one piece of metal to join it to another. Commonly used for attaching patch panels.
Metal Shaping Techniques for Classic Car Panel Fabrication
Shaping metal is where the art of fabrication truly shines. Here are some essential techniques for creating custom body panels:
- Hammer and Dolly Work:
- Purpose: Removing dents, shaping metal around forms, and smoothing welds.
- Technique: Place the dolly behind the metal and strike the metal with a hammer. Use different hammers and dollies for different tasks.
- Tips: Use light, controlled blows. Avoid stretching the metal excessively.
- English Wheel:
- Purpose: Creating smooth curves and contours in sheet metal.
- Technique: Pass the metal between the upper wheel and the lower anvil wheel. Apply pressure and move the metal back and forth to gradually form the desired curve.
- Tips: Start with a gentle curve and gradually increase the pressure. Use a variety of lower anvil wheels for different radii.
- Shrinker/Stretcher:
- Purpose: Shrinking or stretching metal to create curves and flanges.
- Technique: Clamp the metal in the jaws of the shrinker or stretcher and apply pressure to deform the metal.
- Tips: Use small increments and avoid over-shrinking or stretching the metal.
- Metal Bending Brake:
- Purpose: Creating precise bends in sheet metal.
- Technique: Place the metal in the bending brake and use the handle to bend the metal to the desired angle.
- Tips: Use a back gauge to ensure accurate and consistent bends.
- Creating Flanges: Forming a lip or edge on a panel for welding or attachment. Can be done with a bending brake, shrinker/stretcher, or hammer and dolly.
- Forming Curves: Using a combination of techniques to create complex curves and contours. Requires patience and practice.
Choosing the Right Metal for Classic Car Body Panels
The type of metal you choose for your custom body panels is crucial for durability, weldability, and overall appearance. Here are some common options:
- Mild Steel: The most common and affordable option. Easy to weld and shape, but prone to rust. Requires proper rust protection.
- Aluminum: Lightweight and rust-resistant, but more difficult to weld than steel. Requires specialized welding equipment and techniques (TIG welding is preferred).
- Stainless Steel: Strong, rust-resistant, and aesthetically pleasing, but the most difficult to weld. Requires TIG welding and careful attention to heat input to avoid distortion.
- Considerations:
- Thickness: Choose the appropriate thickness based on the panel's function and location. Thicker metal is needed for structural components.
- Gauge: Refers to the thickness of the metal. Lower gauge numbers indicate thicker metal. 18-gauge steel is a common choice for body panels.
- Rust Resistance: If using mild steel, ensure proper rust protection with primer, paint, and sealant.
Step-by-Step Guide to Fabricating a Simple Patch Panel for Classic Car Body Repair
Let's walk through a simplified example of fabricating a patch panel to repair a rusted section of a classic car's fender:
- Assess the Damage: Carefully examine the rusted area and determine the size and shape of the patch panel needed.
- Cut Out the Rust: Use a plasma cutter or angle grinder with a cut-off wheel to remove the rusted section. Be sure to cut back to solid metal.
- Create a Template: Use cardboard or paper to create a template of the area to be patched.
- Transfer the Template to Metal: Place the template on a sheet of metal and trace the outline with a marker or scribe.
- Cut Out the Patch Panel: Use a plasma cutter, shears, or nibbler to cut out the patch panel.
- Shape the Patch Panel: Use a hammer and dolly, English wheel, or shrinker/stretcher to shape the patch panel to match the contours of the fender.
- Test Fit the Patch Panel: Carefully test fit the patch panel in the opening. Make any necessary adjustments.
- Weld the Patch Panel in Place: Use a MIG or TIG welder to weld the patch panel to the fender. Use small, overlapping welds to avoid distortion.
- Grind the Welds Smooth: Use an angle grinder with a grinding disc to grind the welds smooth.
- Apply Body Filler: Apply a thin layer of body filler to smooth out any imperfections.
- Sand the Body Filler: Sand the body filler smooth with progressively finer grits of sandpaper.
- Prime and Paint: Prime and paint the repaired area to match the rest of the fender.
Tips and Tricks for Successful Metal Fabrication on Classic Cars
Here are some additional tips and tricks to help you succeed in your metal fabrication projects:
- Practice, Practice, Practice: Metal fabrication is a skill that takes time and practice to master. Don't be afraid to experiment and make mistakes.
- Start Small: Begin with simple projects and gradually work your way up to more complex ones.
- Use the Right Tools for the Job: Using the wrong tool can make the job more difficult and increase the risk of damage.
- Take Your Time: Don't rush the process. Metal fabrication requires patience and attention to detail.
- Seek Advice from Experienced Fabricators: Don't be afraid to ask for help from experienced fabricators. They can offer valuable tips and guidance.
- Document Your Work: Take photos and videos of your work. This will help you track your progress and learn from your mistakes.
- Invest in Quality Tools: While budget-friendly options exist, investing in quality tools will ultimately save you time and money in the long run.
Safety First Metal Fabrication for Classic Car Restorations
Metal fabrication can be dangerous if proper safety precautions are not taken. Always wear appropriate safety gear and follow these guidelines:
- Wear Safety Glasses: Protect your eyes from flying debris.
- Wear a Welding Helmet: Protect your eyes and skin from the harmful rays of welding.
- Wear Welding Gloves: Protect your hands from heat and sparks.
- Wear Ear Protection: Protect your hearing from the noise of power tools.
- Wear a Respirator: Protect your lungs from fumes and dust.
- Work in a Well-Ventilated Area: Avoid breathing in fumes and dust.
- Keep Your Work Area Clean and Organized: Prevent trips and falls.
- Use Proper Lifting Techniques: Avoid back injuries.
- Disconnect Power Tools When Not in Use: Prevent accidental starts.
- Be Aware of Your Surroundings: Pay attention to what you are doing and avoid distractions.
Resources for Learning More About Metal Fabrication for Classic Cars
There are many resources available to help you learn more about metal fabrication:
- Online Forums: Forums like The H.A.M.B. and MetalMeet are great places to ask questions and share information.
- YouTube Channels: Channels like "Lazze's Metal Shaping" and "Tinsmithing 101" offer valuable tutorials and demonstrations.
- Welding Schools: Local welding schools offer courses in MIG, TIG, and stick welding.
- Metalworking Workshops: Workshops offer hands-on training in metal shaping and fabrication techniques.
- Books: "Metal Fabricator's Handbook" by Ron Fournier and "Sheet Metal Handbook" by Ron and Sue Fournier are excellent resources.
Metal fabrication is a challenging but rewarding skill that can greatly enhance your classic car restoration project. By learning the essential techniques, using the right tools, and following proper safety precautions, you can create custom body panels that are both functional and aesthetically pleasing. So, grab your tools, fire up your welder, and get ready to transform your vision into reality!